U.S. Power Sector Trade Groups Flag Critical Electrical Steel Crunch
Credit to Author: Sonal Patel| Date: Thu, 25 May 2023 14:52:46 +0000
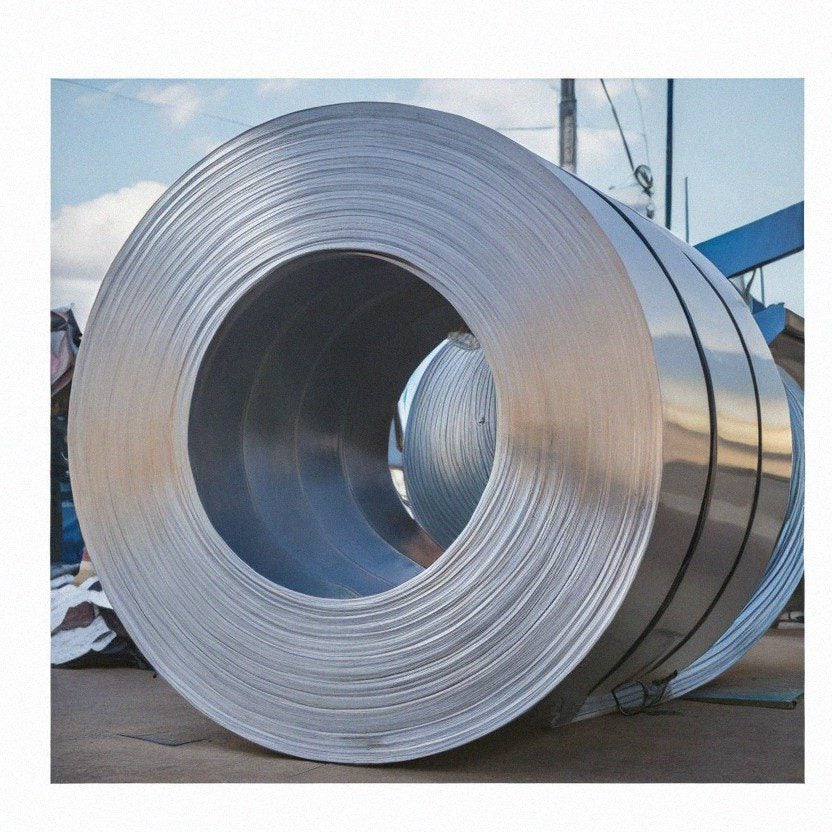
Nine trade groups—including four representing the power sector—have urged the Biden administration to prioritize actions that support the domestic production of electrical steel, warning that shortages are contributing to “significant and persistent” supply chain challenges.
The groups, which include the Edison Electric Institute (EEI), the American Public Power Association (APPA), the National Rural Electric Cooperative Association (NRECA), and the GridWise Alliance, in a letter to President Biden on May 22 said a “sustainable supply” of electrical steel is crucial to U.S. national and economic security.
The letter was also signed by the Alliance for Automotive Innovation, the National Association of Home Builders, Leading Builders of America, the International Brotherhood of Electrical Workers, and the National Electrical Manufacturers Association.
“To deliver on the ambitious goals and visions of the Infrastructure Investment and Jobs Act (IIJA), and Inflation Reduction Act (IRA), it is vital that the federal government recognize and support the domestic production of electrical steel to meet the unprecedented demand for electrification and grid modernization and resilience initiatives,” the groups wrote.
A Critical Need for Electrical Steel
At issue is that domestic demand for electrical steel is at an all-time high. Electrical steel is a flat-rolled silicon alloy—the silicon is added to steel to include increased resistivity, high permeability, and low hysteresis loss. It is also referred to as silicon steel, lamination steel, or transformer steel.
The most prominent categories include grain-oriented electrical steels (GOES), which is cold-rolled grain-oriented steel that typically comprises iron-silicon alloys; and non-grain-oriented electrical steel (NOES). GOES, which is specially rolled and heat-treated to yield a uniformly oriented grain for better magnetic properties, is used mainly for applications that transport and transform mechanical energy into electrical energy—primarily in transformers (where energy or core loss is critical).
The market for GOES in 2020 was primarily dominated by large power transformers (LPT), which are massive critical grid components that can weigh up to 400 tons. NOES, meanwhile, is more commonly used in electric motors and generators, but also in some smaller transformers.
However, domestic access to grain-oriented electrical steels (GOES)—is extremely restricted. The U.S. currently depends on one domestic GOES and NOES producer—AK Steel, a subsidiary of Ohio–based Cleveland-Cliffs, the largest producer of flat-rolled steel in North America. AK Steel produces GOES and NOES at its Butler Works in Pennsylvania and Zanesville Works in Ohio.
However, the company has in past years grappled with sustaining profitability, in part due to years of pressure from low-cost imports of the materials. The Department of Commerce in 2018 imposed a 25% tariff on steel product imports, dramatically tamping down GOES imports. But while Commerce in 2020 initiated another Section 232 investigation into GOES derivative products, it has not acted on its findings.
Outside the U.S., in 2020, Commerce identified 13 GOES manufacturers: four were in China, two in Japan, and others in Germany, India, Poland, the Czech Republic, Russia, Brazil, and South Korea. However, only a limited number of manufacturers are capable of producing high-permeability GOES. In a December 2022 fact sheet, the Department of Energy (DOE) suggested the U.S. is unable to meet domestic demand for new large power transformers (LPTs) with only one domestic GOES manufacturer.
Supply Crunch Affecting Distribution and Large Power Transformers
Compounding the issue is that distribution power transformers (DPT) and LPTs are in critically short supply in the U.S. Power industry stakeholders have suggested that an extended supply crunch, exacerbated by electrical steel limitations, has quadrupled wait times for DPTs, from three to six months before 2022 to one to two years. Wait times for LPTs are currently two years or more.
While power companies have acted to stem potential shortages, an industry-government “Tiger Team” convened to provide the DOE with data on existing distribution transformer stocks suggested 90% of investor-owned electric companies reported a risk of running out “completely” of at least one distribution transformer voltage class within one month. In addition, the Tiger Team’s survey found that lead times to procure distribution transformers had increased more than 400% between 2020 and 2022.
That has direly affected project development. EEI in comments on May 4 noted the survey found 60% of investor-owned companies have had to delay or cancel scheduled projects, owing to a shortage of distribution transformers.
Added Complexity: Looming Transformer Energy Efficiency Standards
Adding even more complexity to the supply chain crunch is that the DOE in December 2022 proposed new energy efficiency standards that seek to mandate amorphous steel cores for almost all distribution transformers produced or imported into the U.S. starting in 2027. Amorphous metal (AM) transformer cores comprise an alloy of iron that includes boron, silicon, and phosphorous in the form of thin foil. According to the DOE, the resulting product is thinner than GOES and has lower core losses, and it reaches magnetic saturation at a lower flux density. The DOE has reasons that AM (which is not widely used in LPTs) would free up competition for core steel supply.
Metglas, the sole U.S. AM manufacturer, during a February 2023 DOE hearing on the rule, noted it currently has an installed AM capacity to produce 45,000 metric tons and can readily increase capacity to another 75,000 metric tons within 30 months. However, during that call (full hearing transcript), Michael Howard, CEO of Howard Industries—the largest producer of distribution transformers in the U.S.—suggested current AM supply capabilities are still sorely lacking. “There is not enough amorphous capacity in the world to handle the market today,” he said.
Howard Industries in supplemental comments submitted to the DOE in March estimated the new standards would result in a 60% increase in demand for silicon steel or an overall increase in demand of 600 million pounds of AM. “The current total available worldwide supply of amorphous is around 400 million pounds, with the total available supply in the U.S. maxing out at just 90 to 100 million pounds,” it said. “ If all amorphous steel is purchased domestically, this translates to a 500% increase in production to meet the demand under the new efficiency standards.”
Other segments of the industry have also vigorously pushed back on the standards. In a March 27, 2023, letter, the American Iron and Steel Institute (AISI) bluntly told the DOE that the proposed rule would have the effect of “requiring all transformers to be redesigned and all manufacturing lines to be retooled to support transformer cores produced from amorphous metal (AM) ribbon in replacement of Grain Oriented Electrical Steel (GOES) by 2027.”
In addition, the group noted: “Amorphous metal is an extremely brittle material that is largely untested and underutilized by transformer manufacturers. Additionally, the existing supply of this alternative material and the substrate needed to produce it is foreign-sourced.”
The group also stressed: “The proposal to replace transformer markets demand for GOES materials with those for AM could result in the elimination of domestic GOES production overall.”
Industry Urges Collaborative Action
In their letter to President Biden on May 22, the nine trade groups underscored the supply chain crunch’s impact on reliability. “The limited availability of domestically manufactured electrical steel poses challenges to the widespread adoption of electric vehicles, delays timelines for utilities to restore power following natural disasters, and is a contributing factor to an insufficient inventory of distribution transformers to meet the demand for new home and commercial construction,” they wrote.
The groups noted that while two unnamed domestic GOES manufacturers have committed to increase GOES production, “even with this expanded output, domestic supply levels will still fall far short to meet electrification goals and satisfy demand created by the IIJA and IRA.” The DOE’s proposed rule, meanwhile, could “upend the market and manufacturing process,” they said.
The groups urged President Biden to work with Congress to “put requisite financial resources toward shoring up domestic supply.” The federal government could “guarantee purchase of GOES and NOES up to a defined amount, as needed by critical electrical industries, to serve a more electrified economy as well as incentivize expanded manufacturing capacity,” they said.
As a first step, the administration could convene an “Electrical Steel Summit” to facilitate a strategic discussion on the current challenges to sustaining and growing domestic production of electric steel, they suggested.
“The Summit would bring together users and manufacturers of electrical steel such as electric utilities, electrical manufacturers, automobile manufacturers, steel manufacturers, labor unions, home builders, and others to help solve the current supply chain crisis that threatens both the national security and economic outlook for the U.S. and to deliver on this Administration’s goals for electrification and decarbonization,” they said.
—Sonal Patel is a POWER senior associate editor (@sonalcpatel, @POWERmagazine).
The post U.S. Power Sector Trade Groups Flag Critical Electrical Steel Crunch appeared first on POWER Magazine.